
Fire protection as a question of existence
Fire protection for conveyor belts
Automatic conveyor systems are the lifeline for many companies. They guarantee continuous flows of material and goods by transporting these items to all areas in the company, through openings in fire walls and ceilings. This is where so-called conveyor system closures are used.
Conveyor systems transport various materials to all areas in the company, through openings in fire walls and ceilings. This is where so-called conveyor system closures (CSC) are used. In the event of a fire, these openings must close automatically and reliably to prevent uncontrolled spread of the fire to adjacent parts of the building.
Three quarters of the companies affected by a major fire do not survive
43% must file for insolvency in the first year - another 28% within the next three years
Investments in fire protection are investments in securing the existence of the company!
For companies, a major fire does not only mean the loss of production facilities or storage facilities. It also has medium and long-term consequences that can be even more devastating. Business incapacity means that the market is reorienting itself. Hard won market shares shrink and loyal customers are forced to buy their goods from other suppliers. If this state of affairs lasts longer, it can lead to a permanent negative change, as customers and competitors do not wait until the shut-down business has recovered. This cannot easily be compensated for by increased investment in marketing. Although fire and business interruption insurance can cover the immediate damage incurred, it usually cannot compensate for damage to the company image or a changing market situation. (Source: bvfa)
Segmentation inside buildings
Statutory requirements
Official building regulations and insurances demand that buildings are split into segments, i.e. into areas separated by fire protection equipment. Openings between these separate areas are always prohibited, unless they are necessary in order to use the building.
If, for example, rail-bound conveyor systems lead through a fire wall, the openings required for this must be provided with self-closing, fire-resistant conveyor system closures (fire resistance at least 90 minutes). The suitability for the use of such closures must be proven in Germany by means of a General Building Inspectorate Approval from the DIBt (in exceptional cases by approval in individual cases) or at European level by a European Technical Assessment. An essential basis for the issue of the proof of suitability are appropriate fire tests. Conveyor system closures must therefore be successfully tested either according to EN 1366-7 (harmonised test procedure) or according to DIN 4102-5 in conjunction with the "Guideline for the approval of fire protection closures in the course of railway-bound conveyor systems" of the DIBt. Both test standards place higher demands on fire protection closures than, for example, DIN EN 1634-1 for doors, gates, closures and windows. For example, the different installation positions of the FAA (close to the floor, elevated wall installation position, horizontal position) result in higher pressures in the fire room than in the test for doors and gates. Furthermore, in the event of fire, the linear expansion and heat conduction of components carrying out the fire or necessary functional gaps of the conveyor system must not have a negative effect on the fire resistance of the closure. The mechanical stress and the durability of the self-closing function of the conveyor system closure must be proven by a continuous function test with 200,000 cycles (Class C5).
A fire protection closure as part of a rail-bound conveyor system must satisfy many requirements!
Parts of a conveyor system closure
Be it a valve construction form, damper construction, swing doors or sectional gate: Today, there is a suitable shielding solution for almost all installation situations and conveyor equipment variants. Each of these CSC must ensure an uninterrupted conveyor process or may not hinder this. Manufacturers of conveyor systems assume that the conveyor system and the CSC work in harmony and ensure a reliable closing process.
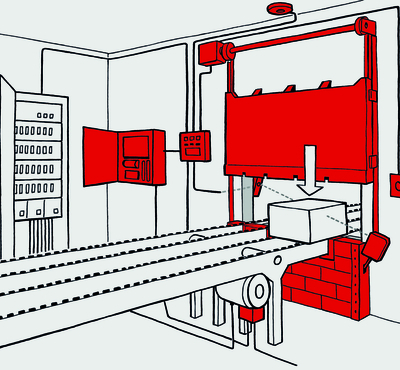
- Conveyor system closures for 22 different conveyor equipment types (interrupted or continuous), e.g. roller conveyor, belt conveyor, suspension chain conveyor, circular conveyor etc.
- Closure tested according to the special standard DIN EN 1366-7 with the much stricter requirements compared to the test norm for gates DIN EN 1634-1 (e.g. high furnace pressure levels, to allow installation in higher positions and the necessary shielding by conveyor equipment etc.).
- tested for various wall types, solid construction types through to lightweight partition walls.
- Control system approved by the building inspectorate (brake systems) that have been specially tested and approved for conveyor system closures (e.g. signal exchange with the conveyor technology).
- Closing areas are cleared when triggered by monitoring the closing areas or clearing systems.
- Ensuring a smooth conveyor process because it is not impacted on by the conveyor system closure.
- Secure shields for continuous conveyor equipment, even in complicated constructions.
- Versatile closing directions due to space constraints.
- Also designed for high function cycles up to 200,000 – and even higher, if required.
- Decentral auxiliary power units for clearing the closing area, also in the event of a power failure.
Versatile conveyor technologies require many shielding variants
Construction forms
Be it a valve construction form, damper construction, swing doors or sectional gate: Today, there is a suitable shielding solution for almost all installation situations and conveyor equipment variants. Each of these CSC must ensure an uninterrupted conveyor process or may not hinder this. Manufacturers of conveyor systems assume that the conveyor system and the CSC work in harmony and ensure a reliable closing process.
The diversity of conveyor system designs today and limiting factors, e.g. space constraints at the installation site and load-bearing capacity of walls and ceilings, are challenging in terms of fire protection concepts. The continuous new developments and improvements of ever more powerful conveyor system closures means that there is a matching shielding possibility for almost all conveyor equipment. If a standard solution is not possible, various customised solutions are possible. Tailor-made to the needs of the intralogistics, modern CSCs guarantee a perfect interaction of conveyed materials, the transport system and the fire protection closure. Intelligent control systems coordinate the clearing of the shield areas, closing of the opening and, if necessary, the auxiliary power supply of the conveyor system in the case of fire.
The issue of the proof of usability based on approved fire tests
Testing and approval of conveyor system closures
The suitability of the use of these kinds of closures must be verified in Germany by means of an approval from the building inspectorate DIBt (in exceptional cases, approval of specific cases, ZiE) or at the European level by means of a European Technical Assessment (ETA).
The essential basis for the issue of the proof of suitability for use is appropriate fire tests. Conveyor system closures must therefore either be successfully tested according to DIN EN 1366-7 (harmonised test procedure) or according to DIN 4102-5 in conjunction with the DIBt guideline for the approval of fire protection closures in the course of railway-bound conveyor systems. Both test standards place higher demands on fire protection closures than, for example, DIN EN 1634-1 for doors, gates, closures and windows. For example, different installation positions of the FAA (floor proximity, elevated wall installation position, horizontal position) result in higher pressures in the fire room than in the test for doors and gates. Furthermore, in the event of fire, the linear expansion and heat conduction of components carrying out the fire or necessary functional gaps of the conveyor system must not have a negative effect on the fire resistance of the closure. The mechanical stress and the durability of the FAA self-closing system must be proven by a continuous function test with 200,000 cycles (Class C 5).